Front duct motor cooling design Project
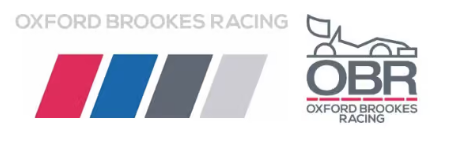
Context
In the pursuit of performance and progress, each year the students of Oxford Brookes University participate in the construction of a Formula Student race car as part of one of the most prolific Formula Student teams. In the quest to improve performance, one of the projects aimed to first determine whether it was possible to convert the water-cooling system of the front motors to an air-cooled system, and second, to assess whether this conversion would lead to a significant improvement in the car's performance.
Learning Outcomes
Technical
This project allowed me to put into practice many of my learning outcomes during my 7 years of engineering studies from heat transfer computation to aerodynamic knowledge. My participation in this project did not just stop in designing a duct with SOlidWorks software that respects the specification required for different condition of operation of the car but I also helped in the numerical evaluation of the product by using thermal and non-thermal CFD simulation on STAR-CCM+ and using appropriate post-processing methods to understand the challenges and improvements needed to increase its performance. Finally, this project was than printed in 3D for track testing were corroboration between measurement and numerical models was necessary to make in order to verify the reliability of our simulations.
Communication
Given the significance of this project, several departments were directly or indirectly involved, requiring effective communication across all of them:
- Suspension: To ensure proper clearance with the suspension system.
- Powertrain: To determine the specifications needed for optimal cooling of the motor.
- Testing: To identify the parameters to measure for numerical validation.
- Lap Time Simulation: To gather essential event-specific environmental data, such as average and maximum speeds.
Créez votre propre site internet avec Webador